Design Control: learn from my mistakes
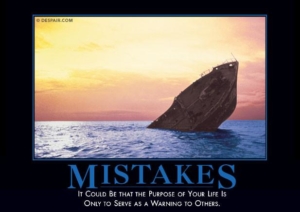
My Mistakes
Years later, I would learn that our first medical device eventually caused unnecessary pain and suffering for many patients and added unnecessary expenses to America’s healthcare costs. In this article, I re-analyze our product using modern design controls, risk management, and the European Union Medical Device Regulation; and I share lessons learned in leadership and entrepreneurship.
Design controls must begin with a plan, so I applied a modern plan to our 2004 product. Like all examples, this is only for discussion of main points, not intended to replace understanding fundamentals. It has many simplifications. Search my blog for other examples, such as an overview of design controls.
Design Plan
This is a simplified example. For the sake of time and ease of understanding, I focus on concepts rather than details.
Scope
References
- Product history
- Risk Management Plan
- Design Controls overview
- Verification & Validation Trace Matrix document, VerVal-TraceMatrix.doc
- Design and Manufacturing Master Validation Plan, DM-MasterVVplan.doc
- Manufacturing processes, ManufacturingProcess.doc
- Manufacturing process validation plan, ManufacturingProcessValidationPlan.doc
- List your quality system policies, standards used or referenced, etc.
Indications for Use

Product Description


Design Input
Design Inputs should include at least two things:
-
- User Needs, including risk management
- Regulatory Requirements, including company policies for design and risk
Your company may include business needs, but should focus on the two main inputs.
User Needs:
- UN#1: Allows faster healing than casts
- UN#2: Has fewer complications than casts
- UN#3: As safe or safer than alternative treatments
User Needs are usually high-level, the same as a person considering that they’d like to purchase an automobile that’s fuel-efficient and inexpensive. User needs are refined to requirements that can be used to design a product to meet their needs, and must include features intended to minimize risk that a user may not be aware of.
Requirements:
- Plate-RQ#1: the plate shall be less than 1.5mm in thickness
- Plate-RQ#2: all corners of the plate shall be rounded to no sharper than 0.25mm radius
- Screw-RQ#1: shall be variable to +/- 20 degrees with respect to the plate holes
- Screw-RQ#2: each screw shall be able to lock into the plate
- ScrewDriver-Risk-RQ#1: The screw driver shall be designed to minimize probability of stripping screws
Risk is sometimes grouped as a separate category, ensuring future teams know which design features addressed risk. Those risk requirements could either be further be refined as unambiguous input requirements, or the generalized requirements could be validated through validation testing and post-market surveillance of assumptions. Generally, requirements should be clear, easy to understand, and unambiguous, i.e. use numbers with values that could be measured in verification testing.
Design Output
- Plate drawing .dwg
- Screw drawing .dwg
- Screw driver drawing .dwg
- Instructions for Use .doc
- Verification Test Protocols .doc
- Validation Test Protocols .doc
You’d add all design outputs, which are all drawings, test methods, instructions, etc. that would be required to satisfy design input requirements.
Verification & Validation
- Verification & Validation Trace Matrix document, VerVal-TraceMatrix.doc
- Design and Manufacturing Master Validation Plan, DM-MasterVVplan.doc
Note to readers:
All design inputs shall be either verified or validated, and many people are confused on the difference between verification and validation.
Verification confirms meeting design inputs by measuring numbers, values, and features that won’t change over time, such as rounded edges called out on a drawing, or the length of screws.
Validation requires testing a representative sample of your product and applying statistics to predict that your results will apply to all designs. In this example, the design input “ScrewDriver-Risk-RQ#1: The screw driver shall be designed to minimize probability of stripping screws” can not be verified, therefore it must be validated with a user test or post-market surveillance of how the screw driver functions in use.
You may prove that all design inputs were either verified or validated by using a master V&V plan, a trace matrix, or this your plan. Just make it easy to follow your logic, ensuring nothing slips through without verification or validation, and that there’s an opportunity to update this plan and all tests based on new information.
Design Transfer
- Verification & Validation Trace Matrix document, VerVal-TraceMatrix.doc
- Design and Manufacturing Master Validation Plan, DM-MasterVVplan.doc
- Manufacturing processes, ManufacturingProcess.doc
- Manufacturing process validation plan, ManufacturingProcessValidationPlan.doc
Device Master Record
- Current or final product,
- All drawing of the parts .doc
- All instructions for use .doc
- All critical features, inspection criteria, etc.
The Device Master record begins as everything defining your product at the moment of design transfer, the version of your product that went through verification and validation testing. It will evolve as products improve or change. Some changes to the Device Master Record document may require that you re-validate the design. Base any decision of whether or not to re-validate based on risk to the patient, and ensure that your plan includes your risk assumptions so that future teams can make risk-driven decisions.
Design History File
- Original design plan .doc
- This design plan .doc
- Histories of each Device-Master-Record.com
- Histories of test data, iterations, etc. maintained in document control
A design history file is simply evidence that you had a plan and followed it, with history of each change to your plan. In this example, I use this plan, updates to this plan, and this section as a design history file.
Continuous Improvement
Lessons Learned
- Any acquiring company must either adhere to the plan or justify why they change it, and all changes must be maintained in their document system for future teams to access.
- Long-term efficiency improves with effective plans. Quick meetings are short-sighted; the time saved moving forward that week costs many months of inefficiency and miscommunications later.
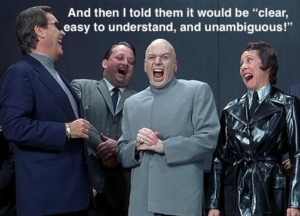