Risk Management: learn from my mistakes
I describe that product in another article. This article helps you learn from my mistakes.
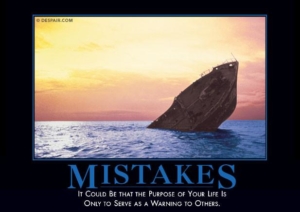
My Mistakes
Years later, I would learn that our first medical device eventually caused unnecessary pain and suffering for many patients and added unnecessary expenses to America’s healthcare costs. In this article, I re-analyze our product using modern design controls, risk management, and the European Union Medical Device Regulation; and I share lessons learned in leadership and entrepreneurship.
I posted the history in another article, Medical Devices: learn from my mistakes, which I suggest reading to help understand and apply the following article about Risk Management and ISO 14971.
Risk Management
Risk management begins with understanding the sequence of events that leads to a hazardous situation, reducing risk of harm in that situation by modifying the product or adding protection, then monitoring and improving your risk management plan. This process must be a continuous part of improving your procedures and product throughout the life of your product, from initial concept to as long as your product is available.
Like all examples, this is only for discussion of main points, not intended to replace understanding fundamentals. It has many simplifications necessary for an online example readable by a broad audience with diverse experience levels.
Risk Management Plan example


The Viper has variable angle locking screws, allowing a physician to select the orientation of a bone screw before locking it to the plate.

References
- EN ISO 14971:2012
- Previous risk documents (you’d find them and list them here, eg. design input documents, PMEA files, etc.)
- Corporate policies and procedures (list policies you follow in addition to EN ISO 14971 to create this plan.)
- Post-market surveillance plan (required if you sell in Europe – link that plan to risk management here)
Hazards


- Sequence of events and hazardous situation: If a screw were not inserted flush with the plate, tendons could be exposed to sharp edges.
- Harm #H1: tendon irritation
- Harm #H2: tendon rupture
Hazard situation #HS2
- Sequence of events and hazardous situation:If a surgeon stripped a screw trying to make it flush with the plate, it could become stuck and require additional surgery time to remove and replace the screw.
- Harm #H2: additional risk from extended surgical anesthesia
- Harm #H3: unnecessary damage to bone during removal and replacement
Acceptable Risk
Risk is severity of harm times probability of harm occurring
- R is the level of risk
- S is the severity of harm
- P1 is the probability of a hazardous situation occurring
- P2 is the probability of harm resulting from a hazardous situation
- P = (P1xP2)
- R = S x P
- R = S x (P1xP2)
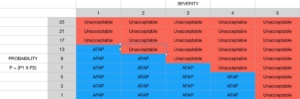
- Inconvenient
- Bleeding or physical damage requiring first aid or less than 20 minutes of treatment
- Visit to an emergency room or treatment between an hour and a day
- Hospitalization under a month or permanent physical damage
- Loss of life or limb
- Rare, < 0.01%, <1/10,000
- Infrequent, 1%, up to 1/100
- Occasional, 1%-5%, up to 5 /100
- frequent, 5%-10% up to 10/100
- probable, >10%, > 1/10
Risk Assessment
- #H1, R1 = 4 x (2 x 3) = 4 x (6)
- #H2, R2 = 3 x (2 x 2) = 3 x (4)
- #H3, R3 = 2 x (2 x 4) = 2 x (8)
- #H4, R4 = 2 x (2 x 3) = 2 x (9)
Risk levels are compared to the risk table. None are unacceptable, all must be reduced as far as possible (AFAP) using risk controls.
Note: Some companies use a separate document for the severity values and acceptability matrix, requiring signatures from senior managers with expertise including clinical, engineering, and quality assurance. This approach protects patients by locking in values that are usually unrelated to product design, and increases efficiency by allowing smaller teams to update the risk plan with lowered probabilities and new hazards; higher-level documents can be updated less frequently.
Risk Control
- an inherently safe design
- added safeguards or protection from harm
- written warnings or instructions
- Written instructions for use, and surgeon training with warnings of the risk
- Added safeguard using a custom drill-guide to align screw holes
- Written instructions for use, and surgeon training with warnings of the risk
- Modified screw driver design to force surgeons to hold the driver more delicately, restricting force of tightening to what is possible with two fingers rather than a full grip.
Monitor and improve

The post-market surveillance plan shall also include both proactive investigation into harm and follow-through with reported incidences of harm, and these percentages shall be used to update this risk management plan.
Similarly, this plan shall update severities at least once every two years and after any documented incidence of a severity of 3 or greater.
End of plan at this point.
Date _________ Signatures _____________ _____________ ____________ ____________
Lessons Learned
- Any acquiring company must either adhere to the plan or justify why they change it, and all changes must be maintained in their document system for future teams to access.
- Long-term efficiency improves with effective plans. Quick meetings are short-sighted; the time saved moving forward that week costs many months of inefficiency and miscommunications later.
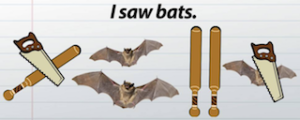
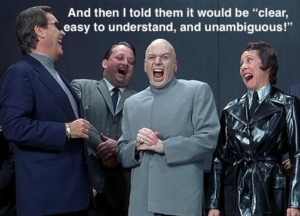